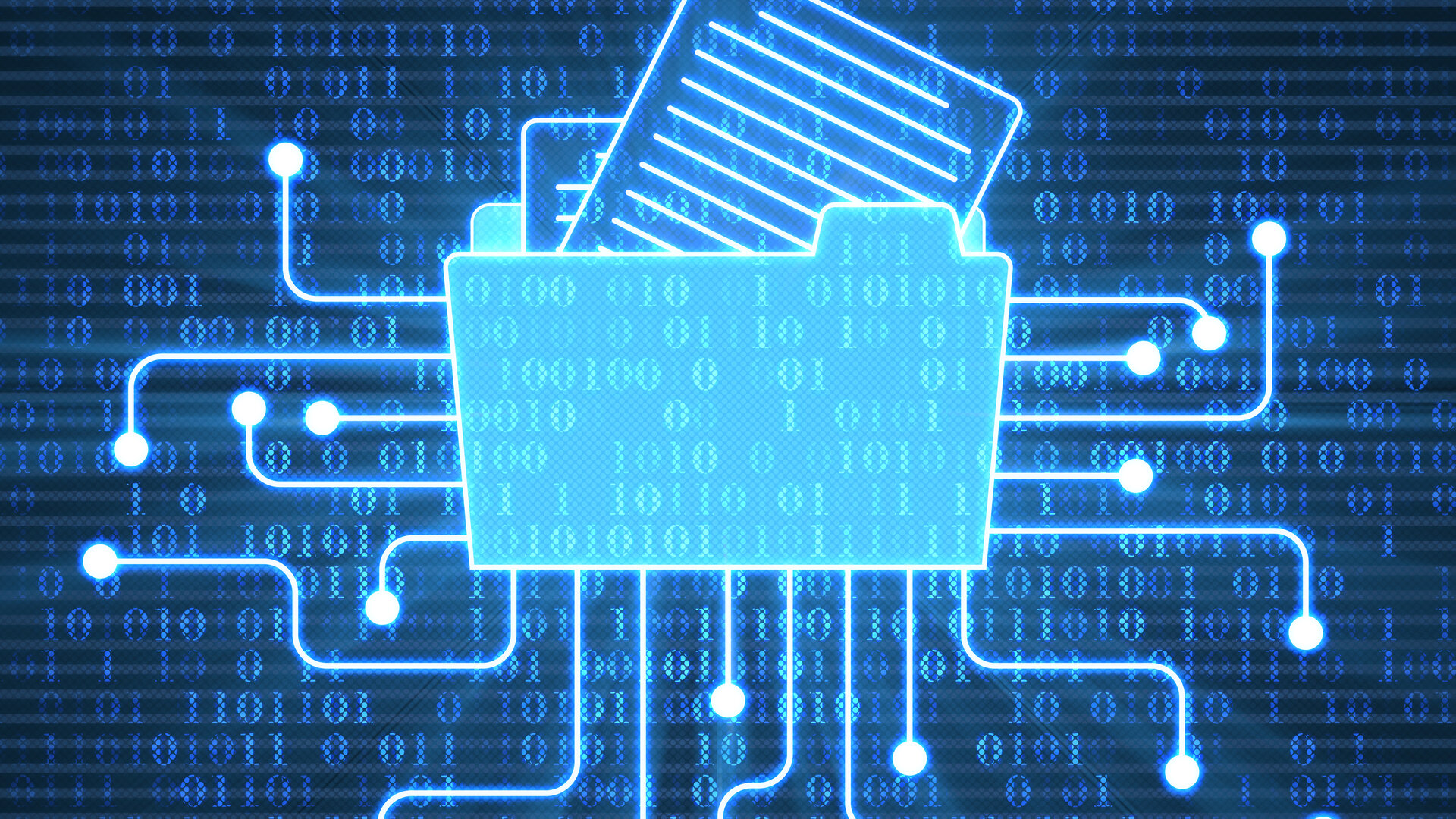
What is Electronic Data Interchange (EDI)?
EDI IntegrationWhat is Electronic Data Interchange (EDI) and what benefits does it offer?
Electronic Data Interchange (EDI) is a key component of modern business processes. EDI digitizes and automates the exchange of business documents—such as orders, despatch advices, invoices, and more—between business partners. The goal is to create more efficient and integrated workflows in the procurement process through automation.
Below are six questions and answers that further explain the fundamentals of EDI, how it works, the benefits for companies, and the role of standards.
What does Electronic Data Interchange (EDI) mean?
Electronic Data Interchange, or EDI for short, is the exchange of electronic business documents between business partners—such as orders, despatch advices, or invoices. The goal is to eliminate manual processes, thereby achieving higher automation and efficiency.
Which business processes can be optimized through EDI?
Typical applications of EDI include the exchange of order data—such as between retailers and manufacturers—and the real-time transmission of electronic invoices. In practice, the process usually starts with the purchase order. Subsequent business documents like despatch advices or invoices are first matched with the order data before being converted into the format used by the business partner and sent electronically. Received invoices are directly checked and processed digitally, allowing any discrepancies to be immediately identified and corrected. Other business processes handled via EDI include, among others, master data management, product specifications, and the processing of payment orders. EDI can also involve third parties in the procurement process by, for example, sending delivery orders electronically to logistics service providers.
What benefit does EDI offer and how can EDI increase the efficiency of business processes?
Through EDI, information is transmitted in real-time, enabling faster planning and processing. Errors that can occur with manual data entry are eliminated, and seamless monitoring of all transactions increases process security. Overall, EDI ensures improved collaboration among all business partners and facilitates production planning through high-quality information. Additionally, it leads to optimized inventory levels, faster response times, and numerous other improvements in business processes.
How does EDI help save money?
Most process costs are eliminated because EDI renders manual data entry obsolete. This frees up employees to focus on core business activities. Automating processes accelerates workflows and improves accuracy and data quality—for example, in warehouse management. This leads to long-term savings. Additionally, using standardized technologies ensures a high level of investment security.
What role do standards play in Electronic Data Interchange?
EDI acts as a bridge to enable communication that is independent of systems (like ERP or inventory management), data formats, communication channels, or media. Standards are crucial for facilitating communication between companies and authorities, even across national borders. Common standards include EANCOM, UN/EDIFACT, ODETTE, VDA, and ANSI X12, as well as typical EDI message standards like ORDERS, DESADV, RECADV, INVOIC, PRICAT, DELFOR, among others.