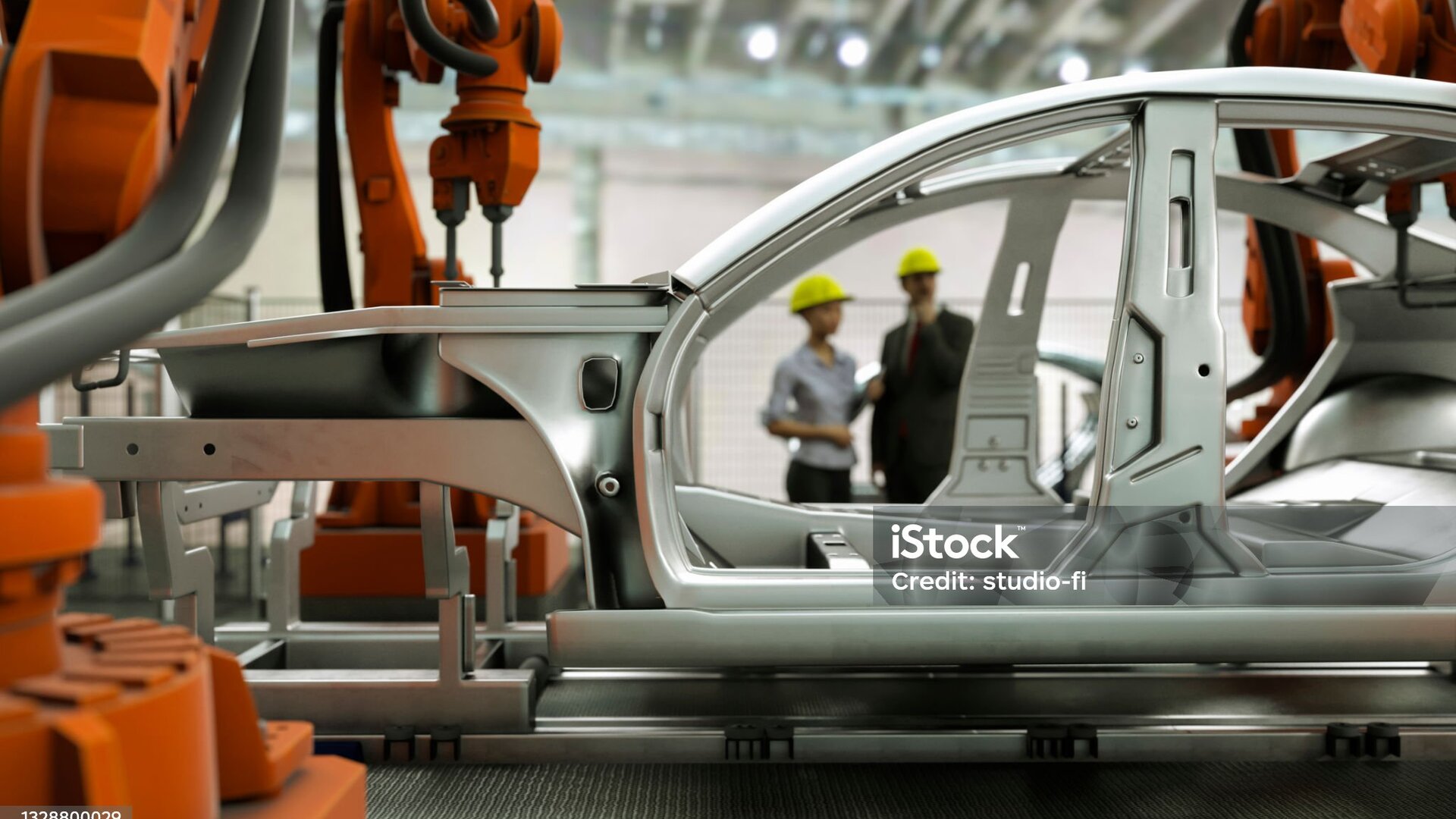
Corporations force
digitization of communications
Corporations are leading the way in digitizing communication processes. Discover how EDI is transforming business operations and driving efficiency.
Interview with Jarosław Trzpiel, Board Advisor for Sales at Editel Polska S.A.
The Czechs have Skoda, the Croats have Rimac Bugatti and the Austrians have Magna Steyr. The Poles do not have an automotive brand, but we are one of the largest manufacturers of automotive parts in Europe. How did this happen in the first place?
During the communist era, we were the largest car manufacturer in the Eastern Bloc after the USSR. In 1980, we produced 417,000 cars, which gave us 13th place in the world and 8th place in Europe. We therefore entered the period of transformation with considerable potential in the form of production facilities and skilled workers. Of course, it was not easy to switch to cooperation with Western concerns, which had completely different requirements in terms of quality, organisation, etc. The prerequisite for finding oneself in the new reality was the transformation of companies, increasing their productivity, investing in employee training. It was also important to adapt in terms of technology. Already at the beginning of the 1990s, companies had to face, for example, the need to adapt to the EDI communication standard. Quite a few succeeded in doing so. I know of an example of a production plant which, before the transformation, supplied parts to a company in Poland and today is a major employer in the region, serving contractors throughout Europe. Before that, it had to modernise thoroughly. There are many, many more similar examples. The strength of these many, often family-owned, factories means that we are actually one of the major component suppliers to the major automotive brands. We have plants in Poland for Fiat, Opel, Volkswagen, Solaris, Man, Volvo or Scania. We supply components ranging from batteries, starters, dashboards, lighting, plating to trailers and bodies.
Is it easy to become a sub-supplier for global brands? I assume it means meeting certain stringent requirements.
Of course, it is not easy. Just getting there is not easy, especially as the automotive supply chain is very extensive. The manufacturer works with sub-suppliers, who in turn work with other suppliers, responsible for the final delivery of parts, etc. A huge challenge, in addition to meeting quality, environmental standards, is therefore to ensure seamless communication with these entities. This is not a matter of a language barrier, but of adapting to standards that have been in place in the Western world for years. We are talking about EDI communication, i.e. the automatic exchange of commercial messages with manufacturers and other sub-suppliers.
For years, the major automotive companies have been using EDI technology and cooperating companies are left with no choice but to follow this path. The concerns that carry out production, on a just-in-time model, want to be able to exchange information with their suppliers seamlessly and in real time. This makes it necessary for them to adapt to these standards. By remaining with a paper-based workflow, they are less likely to establish cooperation.
Is there a single standard for communication and data exchange in Europe, or does each company have its own?
There are different standards for the exchange of information in Europe, which, of course, from the supplier's point of view, complicates compliance with manufacturers' requirements. In Germany, the standard of the Association of the German Automotive Industry VDA is often used. It was introduced by an organisation which brings together
of all car manufacturers who have decided to cooperate with each other, knowing full well that this provides them with the benefits of a more streamlined supply chain and lower costs. In France and other countries, the ODETTE standard is in force, and there are also companies using the EDIFACT standard. As a rule of thumb, a supplier that is expanding has to expect to come across two or three standards for information exchange. But it is not only standardisation that is challenging. Simply implementing EDI in the automotive sector is much more difficult than in, for example, the FMCG or DIY sector.
‘By working with EDITEL, parts manufacturers gain not only access to the largest EDI network in Europe, but also to European know-how based on the implementation of EDI projects ...’ Jarosław Trzpiel
For what reasons?
The Just In Time production model itself is demanding. The second issue is the need to reprocess the DELFOR message, or production forecast. This is a message from the customer to its supplier containing planned dates and volumes for the delivery of goods in the short or long term. In a nutshell: it enables the supplier to plan and manage its resources. It is not usually the case that factory X directly supplies a product to an automotive concern. It generally supplies it to another sub-supplier. An extensive chain of communication is therefore created, in which everyone exchanges information with everyone. Without EDI, this cannot be achieved. But
for EDI to fulfil its function, it must also be integrated into the IT system that manages production. The DELFOR message, or Delivery Forecast, must be understood and processed by the ERP system. This is not easy to do. Although some of the suppliers of these solutions are already capable of processing this message and arranging the logistics process, in Poland, no system manufacturer makes this possibility available as standard. Additionally, as I mentioned earlier, there are different communication standards on the market. There is not one for all. This makes the implementation of EDI much more difficult in the automotive sector than, for example, in the food sector. It takes knowledge and experience to carry out this process successfully.
OK, suppose a company wants to supply its components to a global company, it already has a contract in place. What does it look like from a practical point of view to comply with the commercial information exchange standard?
Companies began to bump up against the problem of adapting to EDI communication requirements in the early 1990s. Initially, automotive manufacturers offered sub-suppliers a portal-based solution. They received a password and login to a website where the DELFOR message was made available in English or German. However, the message was only generated by the concern's factory. It was not possible to issue files externally in front of the sub-supplier. In practice, the workflow was therefore manual and paper-based anyway. When the supplier started supplying products on a larger scale, the situation became more complicated. Logistics had to be rebuilt and, with it, communication in the supply chain.
How can a company implement EDI?
Virtually no one is able to do this on their own today due to the fact that EDI specialists are in short supply and their maintenance is expensive. For this reason, the best solution is to outsource the competence and use companies such as EDITEL.
Which automotive companies does EDITEL work with?
Among others, with Skoda, Futaba, Alpine, and Toyota, for which, in the Czech Republic, we first migrated data to the EDITEL EDI service and implemented 250 suppliers, and then added forecast dispatch advices and invoicing documents. JIT calls via electronic data interchange (EDI) are now also being used. By working with EDITEL, parts manufacturers not only gain access to the largest EDI network in Europe, but also to European know-how based on the implementation of EDI projects in the Czech Republic or Slovakia, where Volkswagen, Toyota or Kia factories are located.